What is Porosity in Welding: Best Practices for Avoiding Permeable Welds
What is Porosity in Welding: Best Practices for Avoiding Permeable Welds
Blog Article
Porosity in Welding: Identifying Common Issues and Implementing Best Practices for Prevention
Porosity in welding is a prevalent issue that commonly goes undetected till it creates substantial troubles with the honesty of welds. This usual issue can endanger the toughness and longevity of bonded frameworks, posturing safety and security threats and causing costly rework. By recognizing the source of porosity and applying efficient avoidance strategies, welders can considerably improve the quality and dependability of their welds. In this discussion, we will certainly discover the vital factors contributing to porosity formation, analyze its damaging impacts on weld performance, and discuss the ideal techniques that can be embraced to reduce porosity occurrence in welding procedures.
Usual Sources Of Porosity
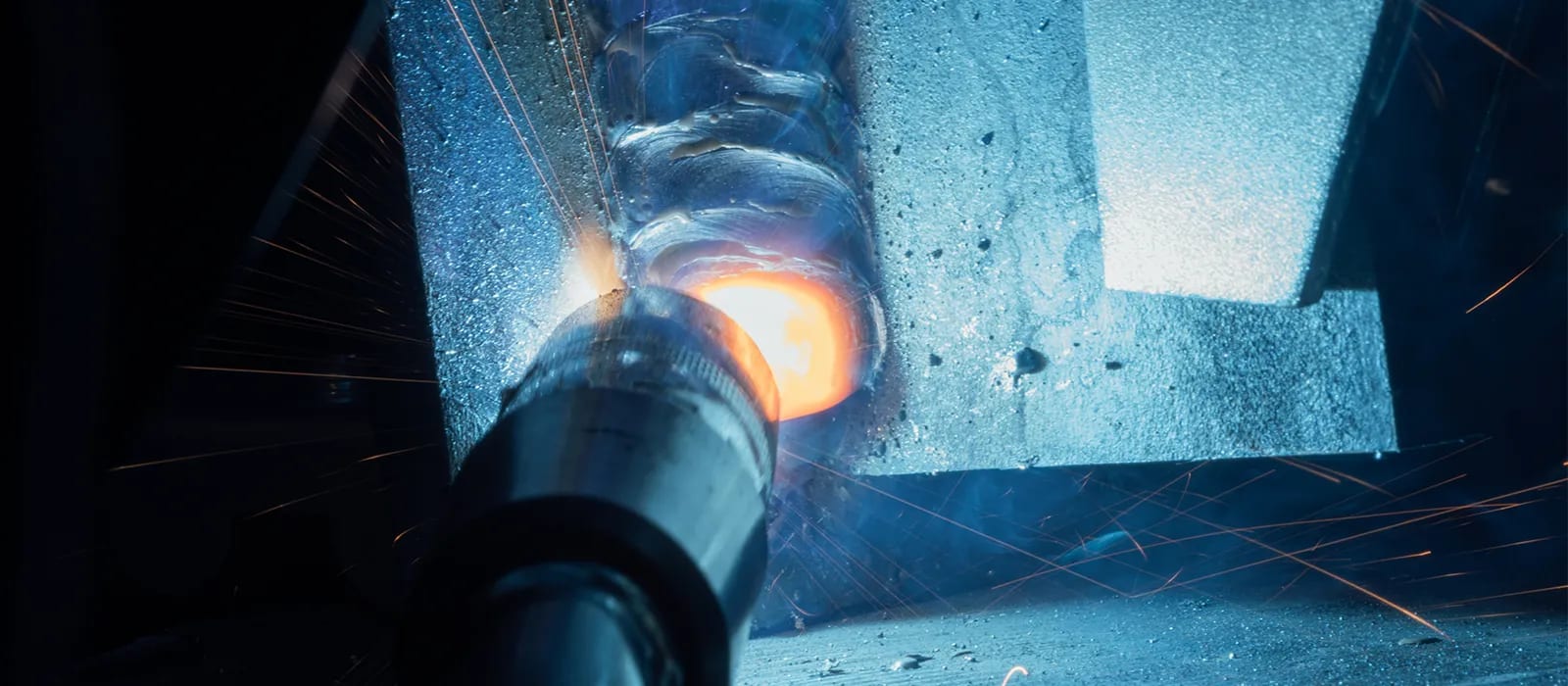
Utilizing unclean or wet filler products can present impurities into the weld, contributing to porosity issues. To reduce these common causes of porosity, extensive cleansing of base metals, appropriate securing gas selection, and adherence to optimal welding specifications are essential methods in accomplishing high-quality, porosity-free welds.
Effect of Porosity on Weld Quality

The presence of porosity in welding can significantly endanger the architectural stability and mechanical residential properties of welded joints. Porosity creates spaces within the weld steel, deteriorating its total toughness and load-bearing capacity. These voids serve as anxiety focus points, making the weld extra vulnerable to fracturing and failure under used lots. Additionally, porosity can minimize the weld's resistance to corrosion and other ecological elements, additionally diminishing its durability and efficiency.
Welds with high porosity degrees have a tendency to show lower effect strength and minimized ability to warp plastically prior to fracturing. Porosity can hinder the weld's capacity to effectively transfer pressures, leading to early weld failing and prospective safety and security dangers in critical structures.
Ideal Practices for Porosity Prevention
To enhance the architectural honesty and high quality of welded joints, what particular steps can be implemented to minimize the event of porosity during the welding procedure? Making use of the correct welding strategy for the particular product being bonded, such as adjusting the welding angle and weapon position, can additionally prevent porosity. Routine assessment of welds and prompt removal of any kind of concerns recognized throughout the welding procedure are vital great site techniques to avoid porosity and generate top notch welds.
Value of Appropriate Welding Techniques
Implementing proper welding methods is vital in making certain the architectural integrity and top quality of welded joints, constructing upon the foundation of reliable porosity prevention actions. Extreme heat can lead to boosted porosity due to the entrapment of gases in the weld pool. Furthermore, using the proper welding parameters, such as voltage, present, and travel speed, is important for accomplishing audio welds with minimal porosity.
Moreover, the choice of welding process, whether it be MIG, TIG, or stick welding, should align with the details demands of the job to make certain ideal outcomes. Correct cleansing and prep work of the base metal, as well as choosing the ideal filler product, are additionally necessary elements of proficient welding strategies. By adhering to you could try these out these finest methods, welders can lessen the danger of porosity development and create top notch, structurally audio welds.
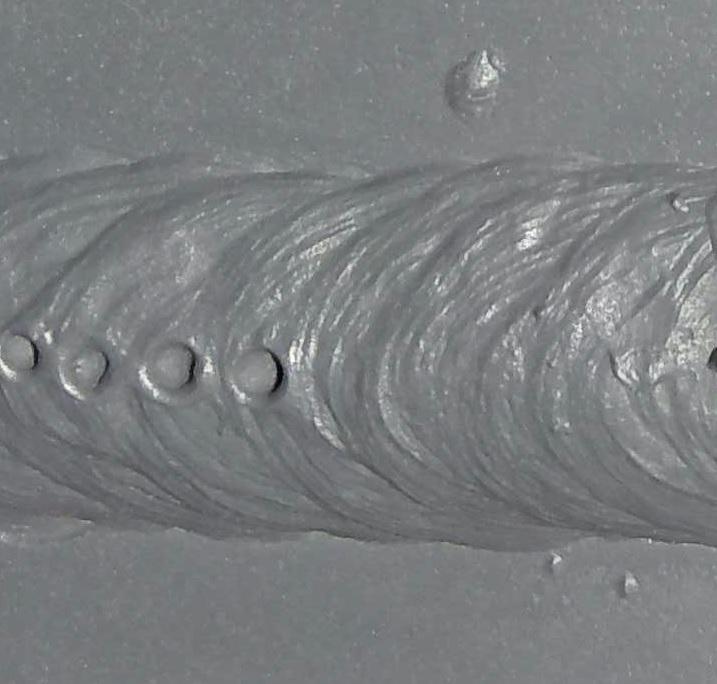
Evaluating and High Quality Control Procedures
Quality control actions play an important function in validating the integrity and reliability of welded joints. Evaluating procedures are vital to identify and prevent porosity in welding, ensuring the strength and resilience of the end product. Non-destructive screening methods such as ultrasonic screening, radiographic screening, and aesthetic examination are frequently utilized to determine prospective problems like porosity. These methods enable for the evaluation of weld quality without compromising the integrity of the joint. What is Porosity.
Conducting pre-weld and post-weld examinations is likewise crucial in keeping quality assurance standards. Pre-weld inspections entail confirming the products, devices settings, and sanitation of the workspace to avoid contamination. Post-weld inspections, on the various other hand, assess the last weld for any issues, including porosity, and validate that it Related Site meets defined requirements. Applying a detailed quality assurance strategy that consists of extensive screening procedures and examinations is critical to lowering porosity issues and making sure the overall high quality of welded joints.
Final Thought
Finally, porosity in welding can be an usual issue that affects the high quality of welds. By identifying the usual sources of porosity and implementing ideal practices for prevention, such as correct welding strategies and screening measures, welders can make certain excellent quality and dependable welds. It is vital to prioritize prevention methods to decrease the incident of porosity and keep the integrity of bonded frameworks.
Report this page